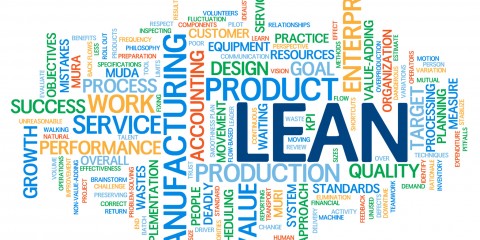
LEAN (lean production, lean manufacturing, бережливое производство)
Нам гораздо проще будет говорить о "бережливом производстве", если Вы, пусть даже из чистого любопытства, прочтете страничку, посвященную "KAIZEN":
Итак, сначала факты:
Система LEAN родилась в результате адаптации японских методов управления к американскому менталитету. Сама методика разработана в ходе исследовательского проекта "Международной программы "Автомобили"" (International Motor Vehicle Program, IMVP) Массачусетского Технологического Института, стартовавшей в 1979 году и продолжающейся поныне. Разработка методики обошлась в 5 миллионов долларов. Руководителями проекта были: Дж. Вумек, Д. Джонс и Д. Рус (J. Womack, D. Jones and D. Roos)
Что же такое LEAN?
Можно сказать, что LEAN - это кайдзен¸ но без «человеческого фактора». Для европейского, тем более – американского, менталитета концепция изменения культуры организации для повышения эффективности оказалась слишком неподъемной. Поэтому, несмотря на всеобщее восхищение Toyota Production System, кайдзен как бы «упростили», свели к набору правил и методик выполнения определенных действий. Причем даже такой подход позволил получить отличный практический результат.
Ключевыми понятиями LEAN являются «ЦЕННОСТЬ» и «ПОТЕРИ»
Ценность – это то, что Вы предлагаете рынку, но с точки зрения потребителя. Компания BOSCH может искренне полагать, что предлагает рынку отличные профессиональные дрели, но потребитель приобретает, на самом деле, удобство и надежность получения дырок. А все то, что не способствует этому процессу – это досадные «примочки», неоправданно увеличивающие цену.
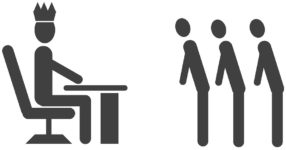
Такой подход к собственным возможностям уже представляет огромную сложность для отечественного бизнеса. Каждый предприниматель уверен, что он предлагает рынку «настоящую вещь», но, по недоразумению, эта «вещь» не находит вполне законного признания у потребителя. Самокритика в таких вопросах у нас не в почете.
Ну а дальше все просто. Если потребитель готов платить только за ценность, то организация должна устранить все потери и затраты, которые не связаны напрямую с получением либо производством этой самой ценности.
Поясняем на примере: если Ваш рабочий шуруповёртом скрепляет две детали некоего изделия, то ценностью для клиента является только их неразрывность, т.е. клиент оплачивает только момент соединения – тот самый процесс и то самое время, когда инструмент загоняет шуруп в деталь. А всё остальное время и все остальные действия (поиск инструмента, анекдот другу, перепалка с мастером, ожидание деталей со склада, уточнение по чертежу, подгонка "по месту", исправление вчерашних "косяков", поход в бухгалтерию и т.д. и т.п.) – это Ваши личные проблемы, глубоко не интересные потребителю. А для Вас это в реальности - оплаченные издержки и недополученная прибыль.
Вот на выявление и минимизацию этих потерь и направлена методическая составляющая LEAN. И если в офисных операциях более эффективным инструментом является «чистый» BPM (Business Process Management), то производство – неисчерпаемое поле деятельности для LEAN.
Какой можно ожидать результат? Смотрим пример:
То есть – потери. Производить не те товары, оказывать не те услуги, делать то и другое не оптимальным способом, совершать при этом лишние действия - это создание потерь. Соответственно, клиент фирмы не испытывает желания вознаградить Вас за их производство. Да и Вам самим они совершенно ни к чему. Правда, просто? Просто, но…
Практика поражает. До 82% (в среднем – 60%) действий и процедур отечественных компаний никак не связаны с получением ценности, т.е. – не влияют на прибыльность и конкурентноспособность. Но это же реально потраченные деньги, усилия и рабочее время!
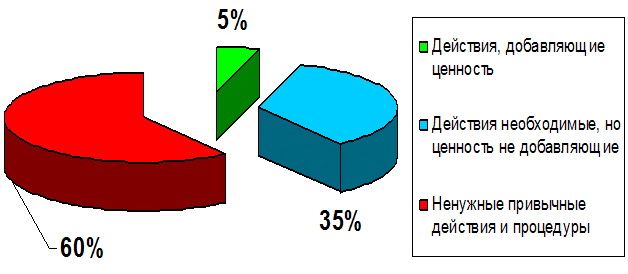
Сборка проблемного изделия "как было":
Сборка изделия после LEAN - мероприятий:
Между этими двумя процессами – четыре месяца работы по методике LEAN двух обученных сотрудников компании при одном консультанте. Оценить разницу по видеороликам может только грамотный технарь или опытный производственник.